Atomic Layer Deposition
Kristina Pitzschel
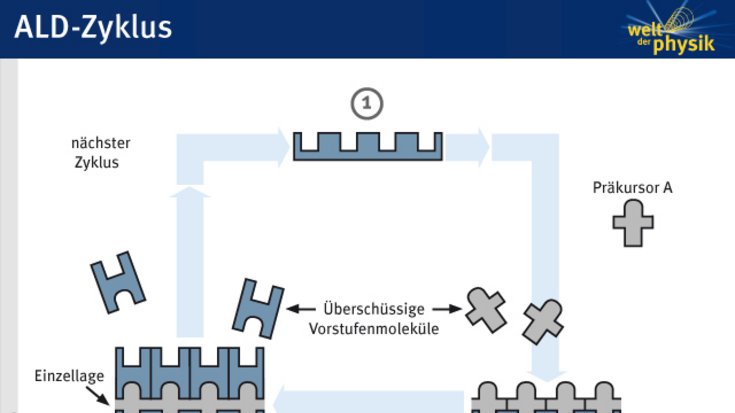
Weniger ist häufig mehr – insbesondere wenn es um die Erzeugung kleinster Strukturen für High-Tech-Anwendungen geht. Das Verfahren der Atomlagenabscheidung ist ein gutes Beispiel dafür. Denn in Atomlagen abzuscheiden bedeutet, die kleinst mögliche Menge einer chemischen Beschichtung zu nutzen.
Erste Anwendungen
Vermutlich nur wenige Besucher des Helsinkier Flughafens waren sich im Jahre 1982 darüber bewusst, dass sie ihre Reiseverbindungen auf einer Weltneuheit präsentiert bekamen: Das erste Dünnfilmelektrolumineszenz (TFEL)-Display der Welt dirigierte die Reisenden zu ihren Flügen. Heutzutage finden sich solche TFEL-Displays in einer weiten Spanne von Anwendungen wieder. Doch egal für welchen Zweck hergestellt, alle TFEL-Anzeigen stellen hohe Anforderungen an das durch einen elektrischen Strom zum Leuchten gebrachte Material.
In den späten 1970er Jahren wurde dafür das Verfahren der Atomenlagenabscheidung (Englisch: Atomic Layer Deposition, kurz ALD) zur Herstellung sehr dünner, qualitativ hochwertiger Schichten von finnischen Physikern entwickelt und eingeführt. Dank des Verfahrens können einzelne Atomlagen mit extremer Präzision großflächig auf ein Trägermaterial aufgebracht werden.
Nachdem sich die ALD zur Dünnfilmherstellung von Displays etablierte, wurde die Methode seit den 1990er Jahren vermehrt für die Herstellung dünner elektrisch isolierender Schichten eingesetzt. „Die ALD ist mit ihrer präzisen Kontrolle und Vielseitigkeit ein unverzichtbares Fertigungsverfahren auf der Nanoskala und wird auch zukünftig an der Verwirklichung vieler neuer technischer Anwendungen beteiligt sein“, ist sich Professor Kornelius Nielsch, Leiter der Forschungsgruppe für multifunktionale Nanostrukturen an der Universität Hamburg, sicher.
Mikroelektronik dank ALD
Wie sich herausstellte, ist die ALD optimal zur Fertigung siliziumbasierter Mikroelektronik geeignet und ist somit für die Computerindustrie von großer Bedeutung. Das Verfahren wird heutzutage vor allem für die Abscheidung dünner Isolatorschichten aus Hochleistungsmaterialien, den sogenannten High-K-Oxiden, eingesetzt. Prominentes Beispiel sind Feldeffekttransistoren, die millionenfach als Hauptschaltelement in jedem Computer vorkommen. Die Transistoren bestehen aus einem Stapel je einer Metall-, Oxid- und Halbleiterschicht. High-K-Oxide zeichnen sich durch bessere Isolationseigenschaften im Vergleich zu den sonst üblichen Siliziumoxidisolatoren aus. Dank dieser Materialien kann eine bessere und genauer einstellbare Isolation und somit eine höhere Leistung jedes Bauelements erreicht werden. Damit die Metall- und Halbleiterschicht des Transistors durch das Oxid elektrisch voneinander getrennt sind, muss die Oxidschicht jedoch äußerst präzise und fehlerfrei gefertigt werden. Mittels ALD können diese Ansprüche mit nur wenigen Atomlagen des Isolatormaterials erfüllt werden, was eine weitere Miniaturisierung der Mikroelektronik ermöglicht.
Mehrstufiger Prozess
Charakteristisch für ALD ist das mehrstufige Verfahren, in dem die Beschichtung schrittweise aufgetragen wird. Die Abscheidung eines Dünnfilms geschieht dabei nicht kontinuierlich, sondern ist von separaten Schritten gekennzeichnet, die während des Prozesses durchlaufen werden. Der Film wächst während eines Beschichtungszyklus um genau eine Lage, man spricht von einem „selbstkontrollierenden Wachstum“. Um weitere Schichten auf der Oberfläche zu stapeln, kann der Wachstumszyklus einfach wiederholt werden. Hieraus resultiert die leichte Kontrolle über die aufgebrachte Schichtdicke.
Technisch werden solche ALD-Zyklen je nach Material in einer Reaktionskammer bei einem Vakuum mit einem Restdruck von einem Pascal – rund ein Hunderttausendstel des Luftdrucks – realisiert. Je nach aufzubringendem Material muss die Kammer auf Temperaturen zwischen 20 und 200 Grad Celsius geheizt werden. Im ersten Schritt wird die Oberfläche in der Kammer reaktiven Molekülen in der Gasphase ausgesetzt. Da die Moleküle beim Reagieren mit der Oberfläche nicht die endgültige Schicht formen, sondern zunächst nur ein Zwischenprodukt bilden, werden sie Vorstufenmoleküle oder Präkursor genannt. Um in die Gasphase gelangen und mit der Oberfläche reagieren zu können, müssen die am Prozess beteiligten Vorstufenmoleküle zunächst einen spezifischen Dampfdruck besitzen. Dieser Dampfdruck muss, gesteuert durch die Temperatur in den Präkursoren, entsprechend hoch sein, um einen effektiven Stofftransport zu gewährleisten. Die reagierenden Stoffe sind Moleküle die als Gase, flüchtige Flüssigkeiten oder als Feststoffe zur Verfügung stehen. Letztere müssen erhitzt werden, um einen ausreichenden Dampfdruck zu erzeugen. Haben die Vorstufenmoleküle mit der gesamten Oberfläche reagiert, ist sie mit einer vollständigen Einzellage eines Zwischenproduktes aus Ursprungsmaterial und Vorstufenmolekül bedeckt. Die erste Stufe des Wachstumszyklus ist damit abgeschlossen und der erste Präkursor wird aus der Kammer entfernt.
Ein zweiter Präkursor wird in die Kammer gebracht und reagiert mit der zuvor gebildeten Zwischenschicht. Dabei bleibt die gewünschte Beschichtung auf der Oberfläche zurück. Ist diese Reaktion auf der ganzen Oberfläche erfolgt, können weitere Präkursormoleküle nicht mehr an die chemisch gesättigte Oberfläche „andocken“. Somit wird auch kein weiteres Material abgeschieden. Aus diesem Umstand resultiert das selbstkontrollierte und leicht steuerbare Wachstum, das ALD auszeichnet. Sind die zweiten Vorstufenmoleküle aus der Kammer entfernt, ist ein kompletter ALD-Wachstumszyklus durchlaufen. Solch ein Zyklus dauert wenige Sekunden, während denen eine Schicht mit einer Dicke zwischen 0,01 und 0,3 Milliardstel Metern abgeschieden wird. Anschließend kann der Zyklus wiederholt werden, um den Dünnfilm mit weiteren Lagen zu verstärken. Die Schichtdicke ist dabei ausschließlich proportional zur Anzahl der Zyklen.
Ein konkretes Beispiel ist die Dünnfilmabscheidung von Zinksulfid, das als Oberflächenbeschichtung zum Leuchten angeregt werden kann. Für die Zinksulfidabscheidung dienen Zinkchlorid und Schwefelwasserstoff als Vorstufenmoleküle, die zu beschichtende Oberfläche ist mit einer Schwefelwasserstoff-Gruppe gesättigt. Zinkchlorid wird als erster Präkursor in die Kammer eingeführt. Dabei geht je ein Zinkatom des Vorstufenmoleküls eine Bindung mit zwei Schwefelatomen der Oberfläche ein. Der Wasserstoff wird durch Zinkchlorid unter Bildung von Salzsäure entfernt. Ist die Oberfläche gesättigt, kann sich kein weiteres Zinkchlorid mehr abscheiden. Im nächsten Wachstumsschritt wird Schwefelwasserstoff als zweiter Präkursor eingebracht. Das an die Oberfläche gebundene Chloratom des ersten Präkursors wird dabei durch Wasserstoff – wieder unter Bildung von Salzsäure – abgeführt. Übrig bleibt eine Einzellage aus Zinksulfid, und die Oberfläche kann in einen weiteren Wachstumszyklus eingebracht werden. Wird der Vorgang wiederholt, so befinden sich zwei Einzellagen Zinksulfid auf der Oberfläche. Die Schichtdicke kann also präzise kontrolliert werden.
Moderne Anwendungen
Moderne Anwendung findet die ALD aufgrund der selbstkontrollierenden Eigenschaft in der Nanostrukturierung. Die ALD ist mit ihren vorteilhaften Eigenschaften eine wichtige Methode zum Beschichten und Erzeugen von Nanostrukturen. Die besonderen Eigenschaften solcher Milliardstel Meter großen Strukturen bergen ein immenses technologisches Anwendungspotential.
So können photonische Kristalle die Ausbreitung des Lichts stark beeinflussen. Sie bestehen aus periodischen Strukturen, die wiederholte Beugungs- und Interferenzphänomene verursachen und dadurch die Bewegung der Photonen durch den Kristall behindern. Die funkelnden Farben von Opalen, Vogelfedern oder Schmetterlingsflügeln sind Beispiele für natürlich vorkommende photonische Kristalle. Die ALD ermöglicht es, solche Strukturen mit Halbleitern, Gläsern oder Polymeren sehr genau künstlich zu erzeugen. Dank der Kontrollierbarkeit des Entstehungsprozesses kann Licht sogar mittels spezifischer Strukturen dazu gezwungen werden, sich in eine gewisse Richtung auszubreiten. Dadurch ist es möglich Funktionen einfacher elektronischer Bauteile mittels Licht zu realisieren.
„Um Rechnerleistungen zu steigern, müssen kleinste Strukturen unter exakter geometrischer Kontrolle angeordnet werden. In diesem Zusammenhang gelang uns die Herstellung magnetischer Strukturen, die nun als potentielle zukünftige Speichermedien untersucht werden“, so Kornelius Nielsch.
Eine poröse nanostrukturierte Oberfläche dient als Vorlage, dem sogenannten Templat, der zu erzeugenden magnetischen Strukturen. Mittels der ALD können dann auf dem Templat Nanoröhrchen mit leicht steuerbaren Parametern wie zum Beispiel variierendem Durchmesser erzeugt werden. Mehrere, nacheinander aufgebrachte ALD-Beschichtungen ermöglichen sogar die Herstellung von Mehrlagensystemen. Für die Röhrchen verwendeten die Forscher der Universität Hamburg zunächst Siliziumoxid, überzogen dieses mit Eisenoxid und brachten zuletzt eine weitere Schicht Siliziumoxid auf. Ähnlich wie der Kunststoffmantel um ein Stromkabel verhindert das Siliziumoxid eine Reaktion der eingebetteten Eisenoxidschicht mit der Luft. Durch diesen Oxidationsschutz werden die magnetischen Eigenschaften des Eisenoxids auch in Flüssigkeiten erhalten. An den magnetischen Nanoröhrchen können Messungen durchgeführt werden, die der Grundlagenforschung dienen und deren Ergebnisse später in der Industrie zur Herstellung von Computerbauteilen angewendet werden könnten.
ALD zwischen Physik und Biologie
Das Verfahren der ALD beschränkt sich jedoch nicht nur auf das Beschichten anorganischer Oberflächen. „Durch die niedrigen Verarbeitungstemperaturen können Dünnfilme besonders schonend abgeschieden werden, wodurch sich das Verfahren auch zur Beschichtung von Biomaterialien hervorragend eignet“, erklärt Professor Nielsch. Die Forscher der Universität Hamburg demonstrierten kürzlich einen weiteren Vorteil des Verfahrens, indem sie auf einer Fliege magnetisches Material deponierten: „Einzig die ALD kann solche sehr komplexen Strukturen präzise beschichten“.
Eine vielversprechende Entwicklung im Forschungsgebiet der ALD ist die Verknüpfung der Biologie mit der Nanostrukturphysik. So gelang kürzlich die Erzeugung von Nanoobjekten aus Biotemplaten wie zum Beispiel Viren und Proteinen. Sogar Spinnenweben können mit ALD behandelt werden, so dass ihre mechanischen Eigenschaften verbessert werden. Solche sogenannten Hybridmaterialien könnten in der Zukunft neuartige Funktionen und Anwendungen übernehmen oder gar erst ermöglichen.
- ALD steht für „Atomic Layer Deposition“, also „Atomlagenabscheidung“.
- Das Verfahren ermöglicht es, auf unterschiedlichsten Substraten gezielt Schichten aufzubringen, die nur wenige Milliardstel Meter dick sind.
- Diese Präzision ist durch sogenanntes selbstkontrolliertes Wachstum möglich, das im mehrstufigen, zyklischen ALD-Prozess realisiert wird.
- In den Gebieten der Elektronik und Nanotechnologie ermöglicht ALD die weitere Miniaturisierung von Bauteilen und die kontrollierte Erzeugung funktionaler Nanostrukturen.
- Großes Anwendungspotential sehen Forscher zukünftig in der Modifikation von biologischen Templaten mittels ALD zu sogenannten Hybridmaterialien.
Quelle: https://www.weltderphysik.de/gebiet/materie/duenne-schichten-und-oberflaechen/atomic-layer-deposition/